That’s a great question; let’s unpack it.
We experienced significant excitement generated by last month's subject, which led to a submission comparing our ChemLINE® Brand of coatings to the widely used solution for rail tank cars currently in use, Rubber Linings.
Transporting hazardous materials requires impeccable safety measures, with rail tank car integrity being a central concern. A recent directive from the Federal Railroad Administration (FRA) has underscored the need for a more reliable alternative to certain rubber linings in rail tank cars, drawing attention to exploring alternative solutions.
This instruction raises the question for rail users to review their selection of lining material and contemplate substitutes for their present lining solution that could provide increased protection and maintenance benefits, such as the ChemLINE® Coating System.
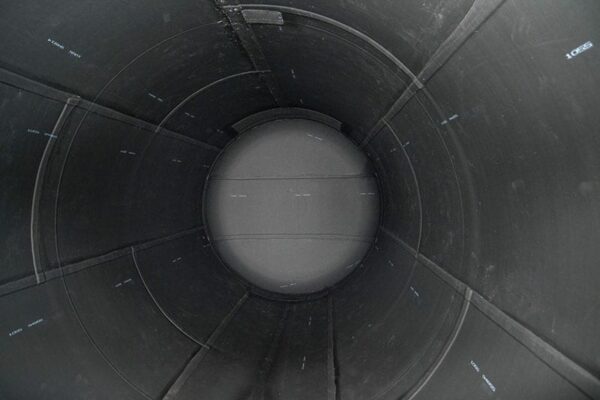
Rubber Linings
Although rubber linings have been a staple for rail tank cars, recent safety concerns and difficulty to repair have left operators looking for suitable replacement options.
Advantages of Rubber Linings:
- Adequate Corrosion Protection: Rubber linings form a protective barrier against corrosive materials, shielding the tank's metal surface from direct contact and mitigating corrosion risk.
- Chemical Compatibility: Rubber linings resist various chemicals, making them suitable for transporting corrosive and reactive materials.
- Flexibility for Movement: The inherent flexibility of rubber linings accommodates vibrations, impacts, and other movements during transportation, reducing the likelihood of cracking.
- Straightforward Application: Rubber linings can be conveniently sprayed or rolled onto the tank's inner surface, ensuring consistent protective coverage.
- Extended Tank Lifespan: Rubber linings significantly prolong rail tank car lifespans by thwarting corrosion-related deterioration.
- Reduced Maintenance: By providing corrosion protection, rubber linings decrease the frequency and intensity of maintenance and refurbishment cycles for rail tank cars.
Disadvantages of Rubber Linings:
- Initial Cost Implications: Adding rubber linings during manufacturing or refurbishment incurs extra expenses, including lining material, application equipment, and labor.
- Maintenance Requirements: Regular inspections and maintenance are vital to preserve lining integrity. Damaged or deteriorated linings necessitate both costly and lengthy repairs or replacements.
- Chemical Compatibility Challenges: Not all chemicals are compatible with specific rubber linings, requiring careful selection to resist transported substances.
- Adhesion Concerns: Proper adhesion of rubber linings to the tank's inner surface is pivotal. Inadequate adhesion can lead to detachment or blistering, compromising the lining's effectiveness.
- Temperature Limits: Rubber linings are constrained by temperature thresholds, with extreme conditions potentially causing degradation and diminishing protective properties.
- Lining Deterioration: Over time, even premium rubber linings can degrade due to exposure to harsh chemicals, temperature fluctuations, mechanical stress, and environmental factors. Regular inspections are crucial to detect deterioration early.
ChemLINE® Coatings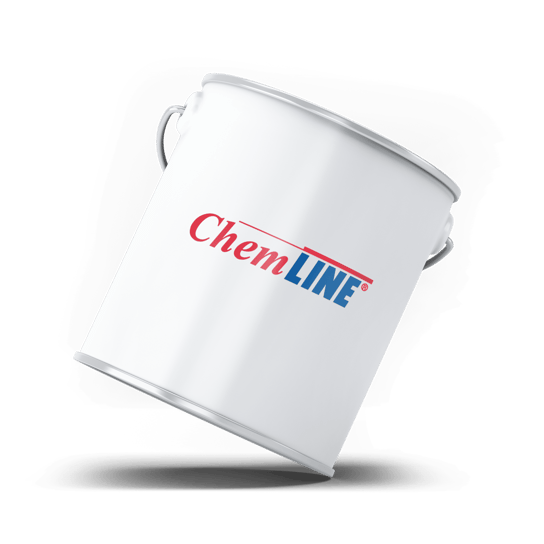
The ChemLINE® Coating System offers a range of compelling benefits that make it a strong contender for lining rail tank cars:
Advantages of the ChemLINE® Coating System:
- Superior Corrosion and Chemical Resistance: Engineered to withstand an extensive array of corrosive chemicals, acids, and solvents, the ChemLINE® Coating System's exceptional chemical resistance minimizes the risk of material degradation and ensures the safe transportation of hazardous cargo.
Some chemicals being moved in rubber-lined cars, which the ChemLINE® Coating System can withstand, include:
-
- Sodium bisulfite (A great case study here)
- 50-70% sulfuric acid
- Sodium Hydroxide
- Ferric Chloride
- Phosphoric Acid
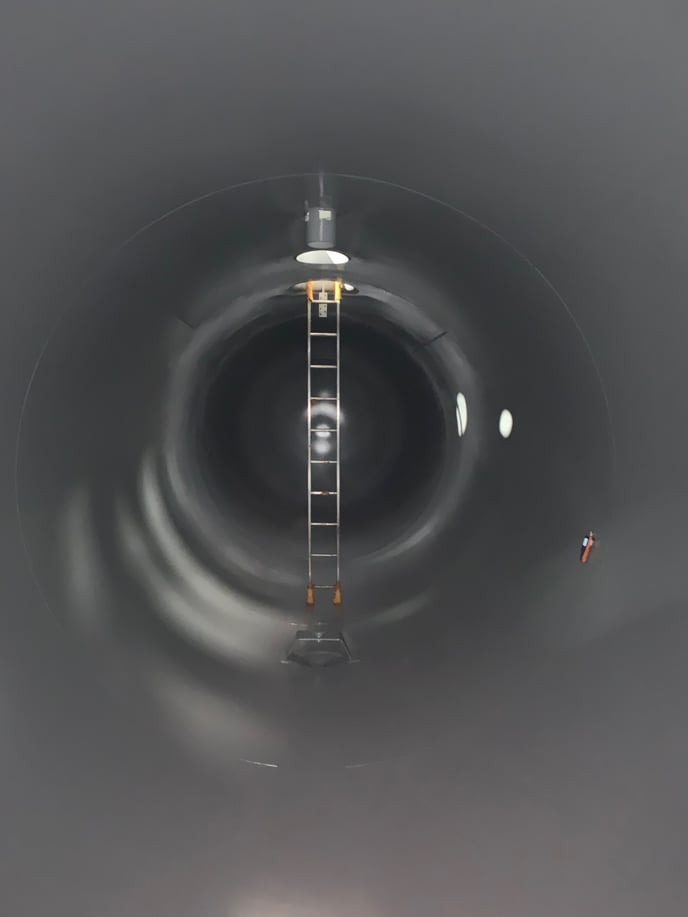
- Unmatched Durability and Longevity: Renowned for its enduring performance, the ChemLINE® Coating System forms a solid and robust barrier, safeguarding against abrasion, impact, and environmental stresses. This enhanced durability contributes to a prolonged rail tank car lifespan.
- Seamless Application Process: Applying ChemLINE® coatings is a streamlined process, requiring minimal labor and time investment. Technical support is readily available for those less familiar with the application, ensuring a smooth transition.
- Practical Maintenance Advantage: The ChemLINE® Coating System's resistance to corrosion and chemicals translates to reduced maintenance requirements for rail tank cars. In situations where maintenance or repair is necessary, ChemLINE® Repair Kits provide a swift solution, allowing repairs on the go.
- Temperature Resilience: Maintaining its integrity across a broad temperature range, the ChemLINE® Coating System guarantees its effectiveness regardless of extreme weather conditions.
- Low Bake Technology: The ChemLINE® Brand of coatings offers a distinct advantage of low temperature, forced-air curing, which alleviates any concern over potential damage to exterior linings and lowers overall application cost.
Disadvantages of the ChemLINE® Coating System:
- Limited Working Time: After mixing, the ChemLINE® Coating System provides a 45-minute window for workability (Pot Life), which imposes a restricted timeframe.
- Necessary Application Safety Gear: To ensure the safety of the applicator from potential epoxy sensitization, it is crucial to adhere to the application procedure and wear appropriate personal protective equipment (PPE) during the ChemLINE® application process. This risk can be easily mitigated by following the Safety Procedures documentation provided with every order of ChemLINE®.
- Curing Duration: While the curing process of the ChemLINE® Coating System is relatively speedy compared to certain coatings, it still demands adequate curing time to achieve its intended complete chemical resistance and mechanical properties. To guarantee optimal performance, railcars coated with ChemLINE® should be allowed ample time for proper curing before being put into active service.
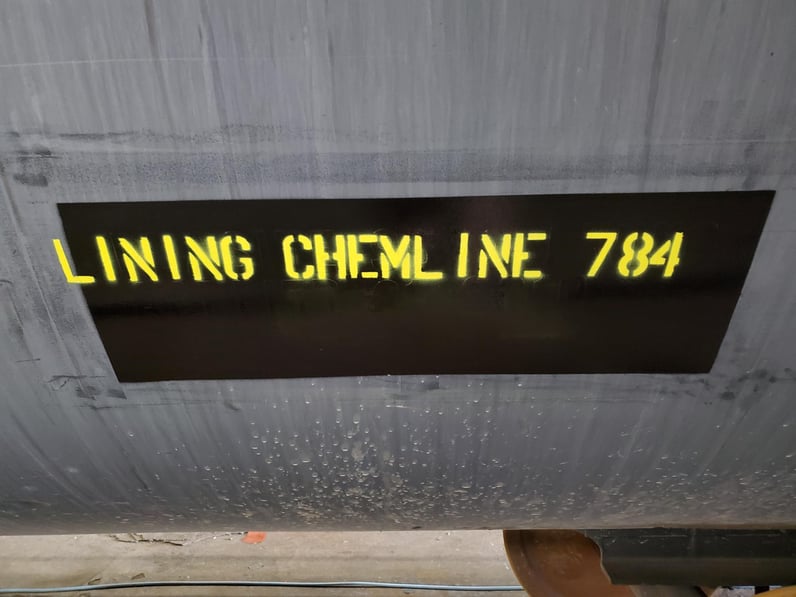
With a focus on public safety and environmental protection, the selection of a suitable lining solution for rail tank cars carries significant weight. Both the ChemLINE® Coating System and rubber linings offer advantages, and the choice between them should be based on specific needs and priorities. The ChemLINE® Coating System presents itself as a strong alternative, addressing the limitations of rubber linings while aligning with stringent safety standards for transporting hazardous materials.
As rail users navigate changing regulations, the ChemLINE® Coating System stands as a compelling option, ensuring regulatory compliance and the utmost safety in rail transport. Given the critical role of rail tank cars in hazardous materials transport, selecting the appropriate lining system becomes a moral and practical necessity to safeguard communities and the environment.
Have something you've been curious about regarding our ChemLINE® and MarineLINE® Coating Systems? If so, click the button below to ask us your questions - and don't worry - this is completely anonymous.
