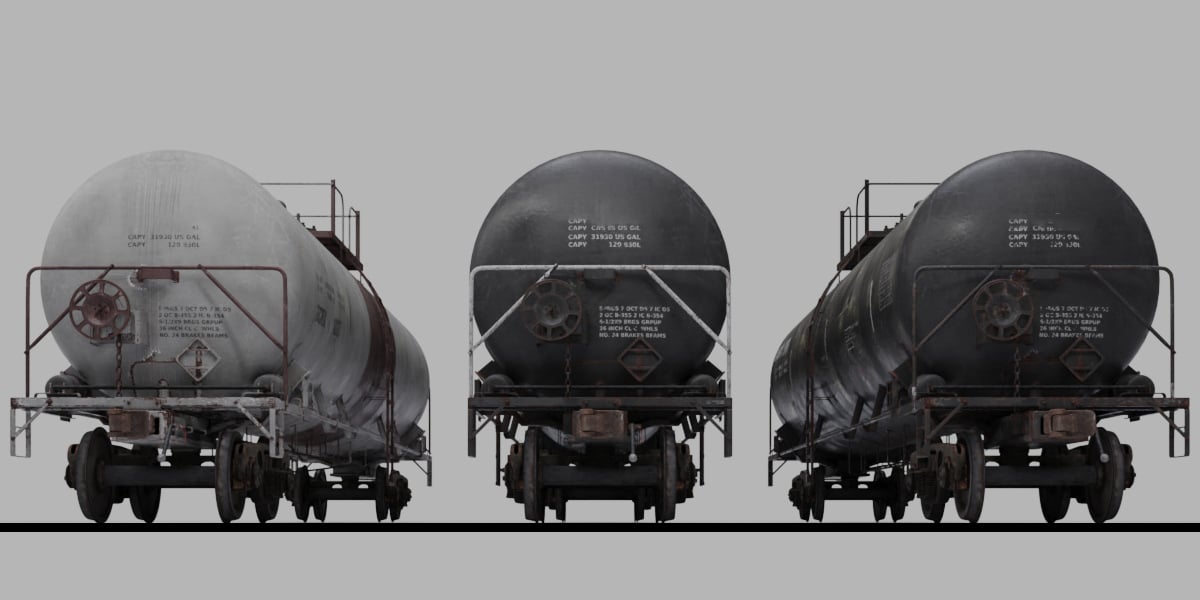
That’s a great question; let’s unpack it.
When it comes to selecting the ideal coating system for rail tank cars, two popular options that often come into consideration are ChemLINE® and Baked Phenolics. Each of these coating systems brings its own set of advantages and disadvantages to the table. ChemLINE® is renowned for its exceptional chemical resistance, flexibility, and extended service life, while Baked Phenolics offer outstanding durability, heat resistance, and cost-effectiveness. This article will delve into a comparative analysis of these two coating systems, exploring their strengths and limitations to help you make an informed decision for your railcar application needs.
Baked Phenolic Coatings
Baked Phenolic Coatings are commonly applied using spraying and baking methods. The process involves spraying the coating onto the substrate and subsequently heating the coated substrate in an oven to cure the coating, facilitating the chemical cross-linking of phenolic resins and forming a tough, chemically resistant coating material.
Advantages of Baked Phenolic Coatings:
- Lower Upfront Cost: Baked phenolic coatings offer lower upfront costs than other coatings, primarily because phenolic resins, the critical component of these coatings, are generally more affordable than different types of resins used in coatings. The lower cost makes baked phenolic coatings an attractive option for applications where budget constraints are a concern.
- Application in Thin Films for Better Flexibility: Baked phenolic coatings can be applied in thin films, providing better flexibility than thicker coatings.
- Excellent Resistance to High Dry Temperatures: One of the notable advantages of baked phenolic coatings is their excellent resistance to high dry temperatures. Phenolic resins have high thermal stability and can withstand elevated temperatures without significant degradation.
- Good Chemical Resistance to Acids and Other Chemicals: Baked phenolic coatings exhibit good resistance to acids and other chemicals.
- Effective Abrasion Resistance and Durability: Baked phenolic coatings offer effective abrasion resistance and durability. The phenolic resins in these coatings form a hard, protective surface that can withstand mechanical wear and tear.
Disadvantages of Baked Phenolic Coatings:
- High Heat Requirement: Baked Phenolic Coatings necessitate a significant amount of heat (400°F, 204°C) to ensure proper curing.
- Potential Damage to Exterior Paint and Stenciling: The high heat in the baking process can harm the exterior paint and stenciling on railcars or other coated surfaces.
- Challenging Repair Process: Repairing Baked Phenolic Coatings is a complex and challenging task. Often shops use low-bake linings to attempt repairs, which end up incompatible with the chemical they’re transporting, ultimately resulting in an ineffective repair.
- Limited Resistance to High pH Chemicals: These coatings exhibit less resistance to chemicals with high pH levels.
- Presence of Phenol, a Hazardous Chemical: Baked Phenolic Coatings contain phenol, a hazardous substance.
- High VOC Emissions: These coatings release high levels of volatile organic compounds (VOCs) during application.
- Limited Shelf Life: Baked Phenolic Coatings have approximately six months of shelf life.
ChemLINE® Coatings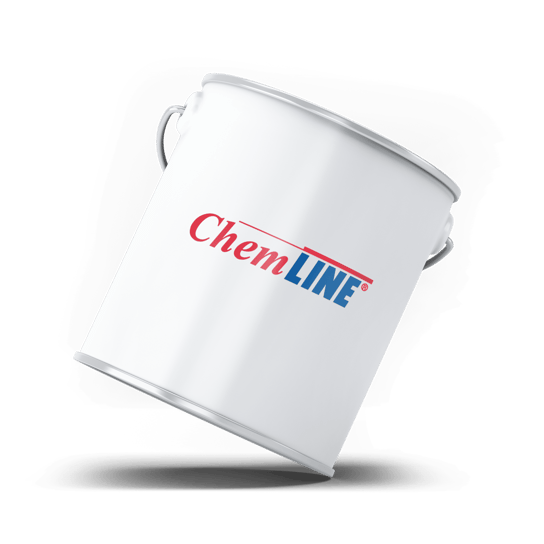
ChemLINE® Coatings have emerged as a leading choice in the railcar industry for their exceptional protective qualities and versatility. The ChemLINE® coating process involves the application of a specialized formulation that creates a chemically resistant barrier on the substrate. Unlike traditional baking methods, ChemLINE® coatings undergo a chemical curing process that forms strong molecular bonds, resulting in a durable and robust coating material. With its proven track record in safeguarding against a wide range of aggressive chemicals, ChemLINE® has become synonymous with reliability and longevity in railcar applications.
Advantages of the ChemLINE® Coating System:
- Chemical Resistance: ChemLINE® offers exceptional resistance to a wide range of aggressive chemicals, including acids, alkalis, solvents, and corrosive substances. This feature ensures the protection and integrity of the tank, reducing the risk of chemical attacks and leaks during transportation.
- Flexibility and Compatibility: ChemLINE® is a multifunctional coating system providing flexibility in handling various types of chemicals. It is compatible with different tank designs and materials, including carbon steel, stainless steel, and fiberglass-reinforced plastic (FRP). This versatility allows for greater adaptability in diverse railcar applications.
- High-Temperature Resistance: The ChemLINE® system exhibits excellent resistance to high temperatures, making it suitable for transporting hot substances. It can withstand thermal cycling and maintain its protective properties even under extreme temperature conditions.
- Low Maintenance and Extended Service Life: ChemLINE®'s durable and robust formulation minimizes the need for frequent maintenance and re-coating. It offers an extended service life, reducing downtime and associated costs. This advantage makes it an attractive choice for railcar owners and operators seeking long-term reliability and cost-effectiveness.
- Easy Application and Fast Cure Time: The ChemLINE® coating system is designed for easy application, allowing for efficient and consistent coverage of tank surfaces. It has a relatively fast cure time, reducing the overall coating process duration and facilitating quicker return-to-service of rail tank cars.
Disadvantages of the ChemLINE® Coating System:
- Initial Cost: The ChemLINE® system may have a higher initial cost compared to some conventional coatings. However, long-term benefits, such as reduced maintenance and extended service life, often offset this cost.
- Limited Pot Life: The ChemLINE® system offers a 45-minute pot life after mixing, which could create a limited time frame for workability.
- Proper Application PPE: When applying ChemLINE®, following the application procedure and wearing proper PPE is essential to protect the applicator from possible epoxy sensitization. This is easily avoided by following the supplied Safety Procedures documentation included in every ChemLINE® order.
- Cure Time: While the ChemLINE® system has a relatively fast cure time compared to certain coatings, it still requires sufficient curing to reach its full chemical resistance and mechanical properties. Railcars coated with ChemLINE® should be allowed proper curing time before being put into service to ensure optimal performance.
It is important to note that the advantages and disadvantages of the ChemLINE® Coating System may vary depending on specific application requirements, operating conditions, and industry standards. Conducting a thorough evaluation and considering these factors will help make an informed decision regarding the suitability of ChemLINE® for railcar coating applications.
The ChemLINE® Coating System and Baked Phenolic Coatings offer excellent chemical resistance and performance in harsh environments. The choice between the two would depend on specific application requirements, such as the types of chemicals involved, operating temperatures, and desired coating properties. Consulting with coating experts or manufacturers would be advisable to determine the best option for a particular use case.
Have something you've been curious about regarding our ChemLINE® and MarineLINE® Coating Systems? If so, click the button below to ask us your questions - and don't worry - this is completely anonymous.
