That’s a great question; let’s unpack it.
Sharp edges, external corners, crevices, and welds represent vulnerable zones where coating failures and corrosion often originate. This vulnerability arises primarily due to inadequate coating protection caused by reduced coating thickness, a consequence of surface tension during the curing process of wet coatings. This tension forces the coating material to contract and retreat from these critical areas, exposing them to corrosion.
This phenomenon is particularly prevalent at the edges of entry points into tanks, such as manways, fill areas, baffles, and much more, making them potential trouble spots. When the coating deteriorates in these regions, it sets the stage for significant corrosion issues that can rapidly expand beyond the initial affected area if not promptly addressed.
In the context of coating processes, edge retention becomes a pivotal concept. It refers to a technique that ensures a sufficient amount of protective coating material is applied to the edges of materials prone to corrosion or rust. Typically quantified as a percentage, edge retention measures the coating on an edge compared to the coating remaining on an adjacent flat surface.
Edge retention is a critical consideration when selecting a coating system, especially when transporting hazardous materials and chemicals. The unique challenges and safety considerations associated with such applications underscore the importance of maintaining the integrity of coatings at vulnerable edges and corners.
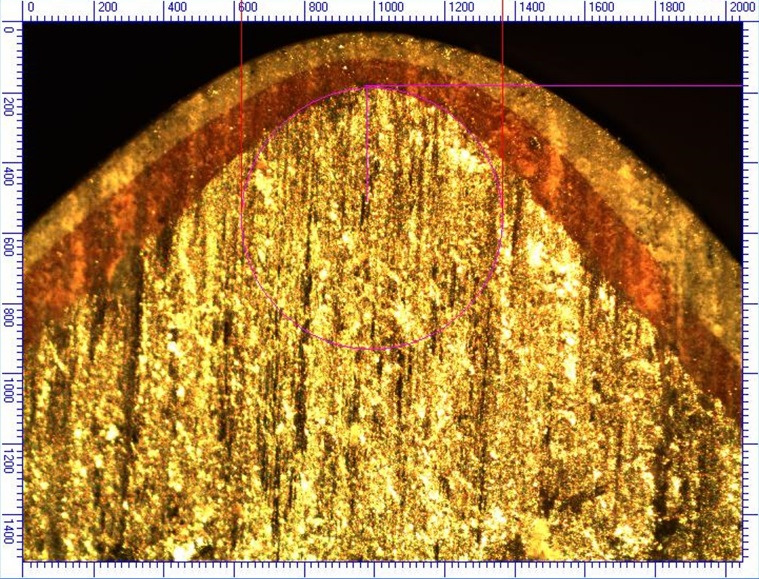
To combat issues related to poor edge retention and the potential for corrosion, ChemLINE 784 stands out as a highly recommended solution. Recent studies conducted by APC's R&D team have showcased exceptional edge retention results for the ChemLINE 784 coating system.
Remarkably, ChemLINE 784 surpasses the stringent requirements set by industry standards, boasting an average edge retention rate of 71.4%. This impressive performance ensures robust protection for the underlying substrate.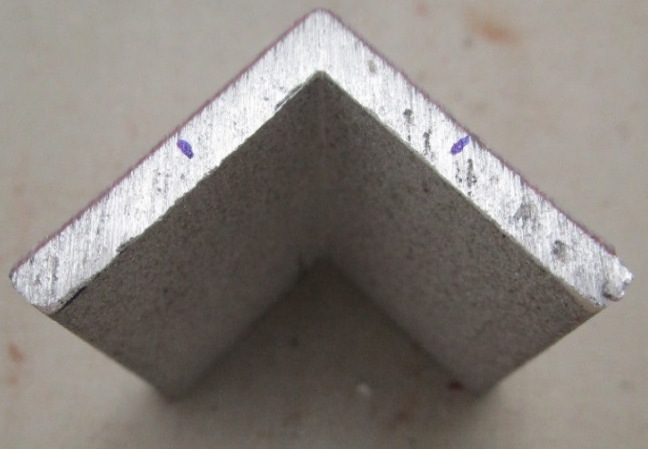
Furthermore, the advantages of ChemLINE coatings extend beyond their superior edge retention. They also exhibit high chemical resistance, making them well-suited for applications involving corrosive substances. Additionally, these coatings are known for their ease of maintenance, reducing the burden of upkeep.
In the event of mechanical damage inside a lined tank, the availability of Repair Kits further enhances the appeal of ChemLINE coatings. This feature ensures field repairability, minimizing downtime and potential risks associated with coating damage.
The concept of edge retention is a critical aspect of coating processes, especially when dealing with hazardous materials and chemicals. Choosing a coating system with excellent edge retention, such as ChemLINE 784, not only safeguards against corrosion but also offers chemical resistance and ease of maintenance, ultimately contributing to the longevity and efficiency of various industrial applications.
Have something you've been curious about regarding our ChemLINE® and MarineLINE® Coating Systems? If so, click the button below to ask us your questions - and don't worry - this is completely anonymous.
