Yet another excellent question here. Thanks for submitting.
Some of the most commonly asked questions about our patented polymer coating systems pertain to "how" the technology behind the coating does what it claims to do - and we love answering them.
This question, particularly, brings up a great article written by APC Founder Donald J Keehan a handful of years ago, featured in Tanker Operator Magazine.
To answer the question in short: The higher the crosslink density, the lower the absorption rate.
Read on...
When customers ask how the patented MarineLINE® cargo tank coating keeps chemicals pure from port to port, the discussion leads to a basic understanding of the chemistry behind polymers.
These are the basic building blocks used in high-performance coatings.
Most coatings have adsorption and absorption qualities based on the crosslink density of the polymer used.
- Adsorption is a surface condition and can be removed easily.
- Absorption is the penetration of chemical molecules into the molecular structure of the coating.
Absorption is more difficult to remove and requires long drying times and/or chemical cleaning. Absorption also depends on whether the coatings' molecular structure is open or closed. In polymer chemistry, this is called crosslink density of the cured polymer.
The higher the crosslink density, the lower the absorption rate. A simple analogy is to compare chicken wire to mosquito screen. The chicken wire keeps the chickens in but also allows flies and mosquitos to enter. The mosquito screening also keeps the chickens in but does not allow flies and mosquitoes to enter.
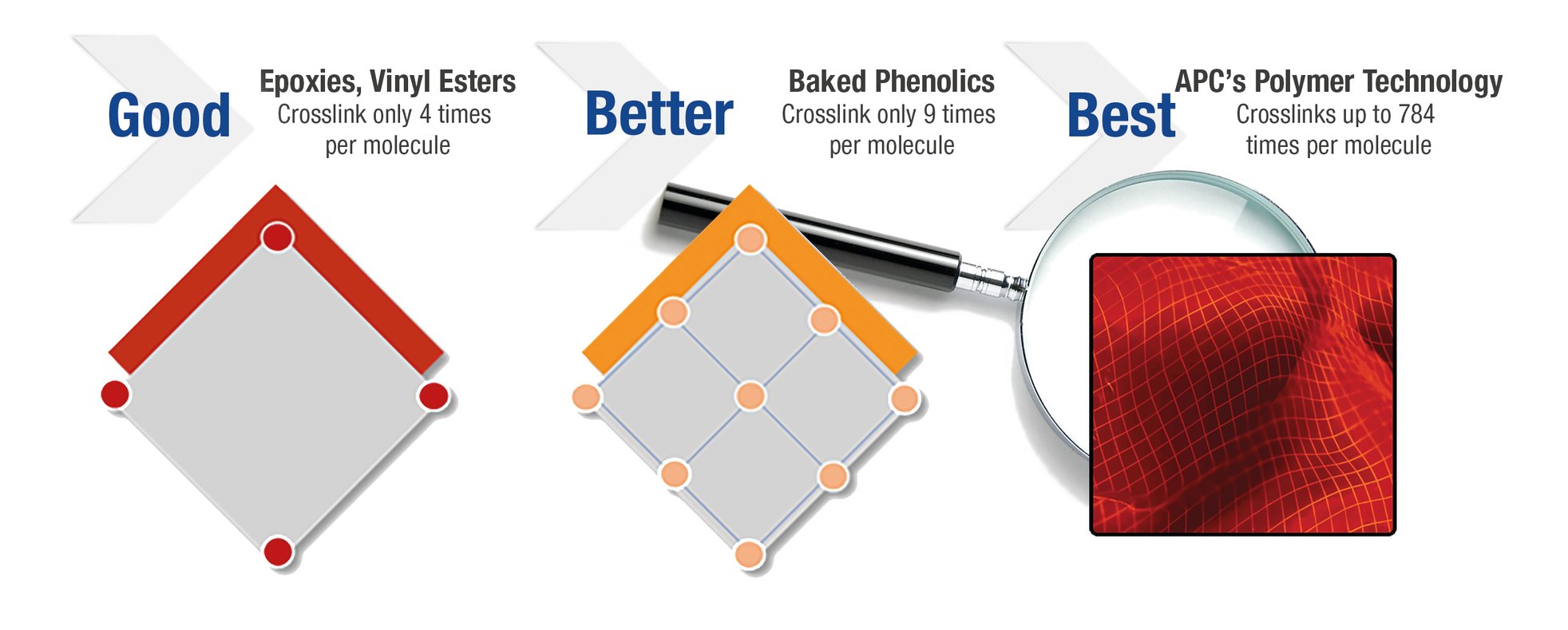
Thus, a higher crosslink density coating is like the mosquito screen, as it keeps out large and small chemical molecules, such as acids, solvents, etc., effectively protecting the underlying surface. To get the highest crosslink density, the polymer must be fully cured, as presented in the illustration above, where a higher crosslinking density is shown in a cured coating.
Standard Phenol epoxies never really obtain a complete cure, even over an extended period. The crosslinking density depends on the type of epoxy used and the curing agent/hardener used. The higher the functionality of the epoxy, the higher the crosslinking.
Functionality is the number of Oxirane/epoxy end caps that can be crosslinked with the curing agent. The initial reaction between the epoxy end caps and the curing agent creates exothermic heat, a chemical reaction that releases heat, which helps molecules rotate around to find unreacted end caps.
As the structure polymerizes (hardens), it becomes more difficult to crosslink the epoxy end caps that become unreachable, even over long periods. Some epoxy end caps do not crosslink, which could be as high as 30% in some cases.
Advanced Polymer Coatings (APC) research chemists have found that heat is required to get the highest crosslinking percentage in the MarineLINE® coating system (96 to 100%) to force the hard-to-reach epoxy end caps to crosslink.
Heat curing early in the crosslinking (polymerization) stage helps keep the molecules mobile and forces them to crosslink to form a tightly knit structure.
Once the polymer crosslinks, at atmospheric temperature, to a certain point (75 to 85%), then over time, it becomes almost impossible to force crosslinking unless a significantly higher temperature is used than required in the early stage of polymerization. That is why heat curing during the early stage of polymerization is essential.
APC places a very high focus on proper heating curing of MarineLINE® to create a high crosslink density, thus creating a smooth, virtually impermeable coating barrier between the steel tank and the chemicals carried. This is key to maintaining the purity of the chemical cargo carried.
Check out a real-world example of actual cargo sequencing from a ship owner operating a MarineLINE® coated vessel...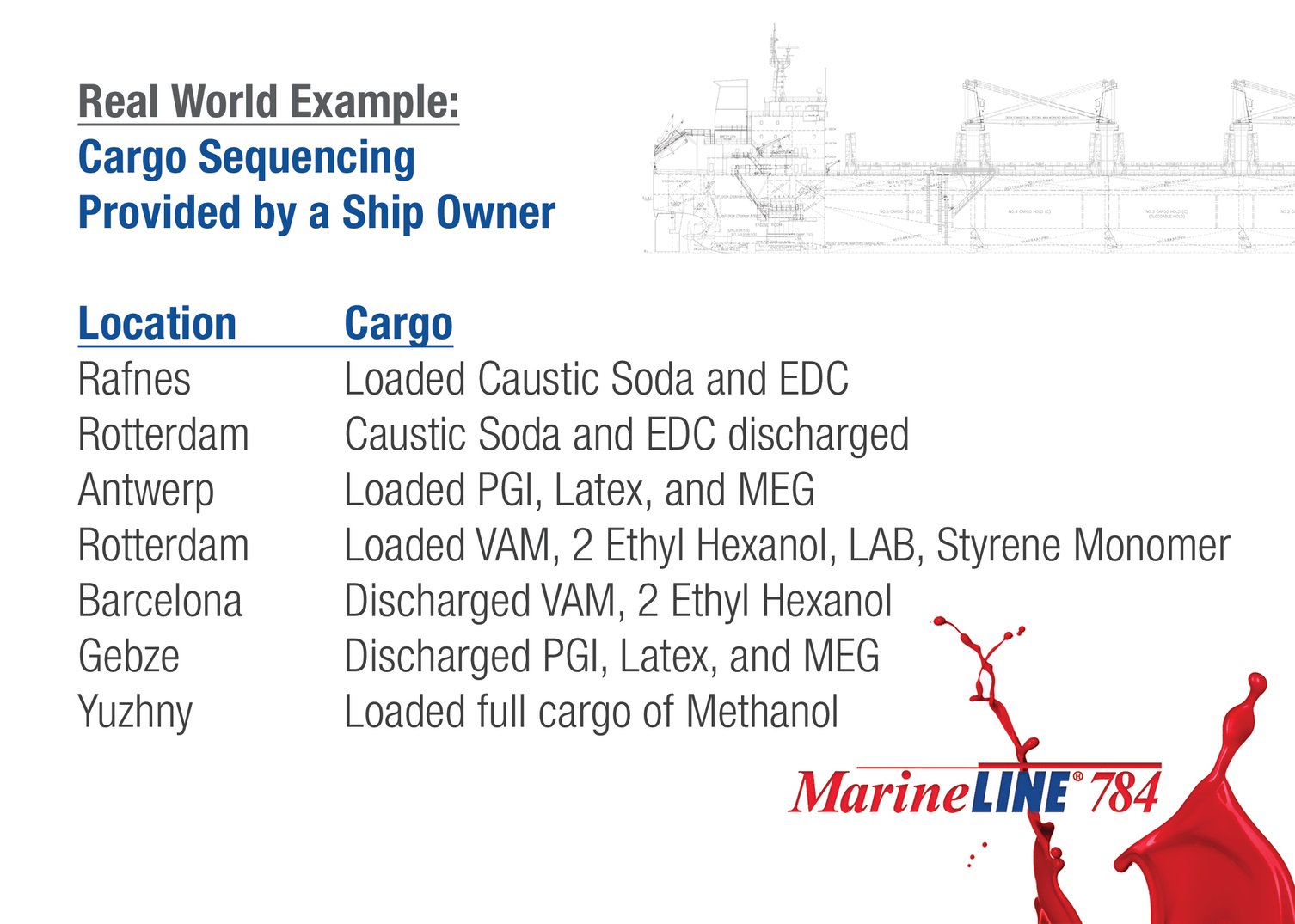
Ongoing coating maintenance and proper tank cleaning (tank decontamination from previous cargo carried) are also essential components of any cargo tank purity discussion. Typically epoxy and Phenol epoxy coatings absorb solvents and other chemicals and may take a long time to dry out. They may also require extensive use of cleaning chemicals to wash the coating surface thoroughly.
However, for the higher crosslink density MarineLINE® coating, the entire cleaning operation is faster and easier, as cargoes do not permeate the coating, according to shipowners using MarineLINE® cargo tank coatings. When/if needed, approved cleaning detergents are provided on the APC website for MarineLINE® and a complete cargo resistance list.
The takeaway?
*Selecting the best cargo tank coating is paramount for purity success because - the higher the final crosslink density, the less cargo absorption and the less possibility of cargo contamination.*
Are you interested in having your questions answered? Click the link below!
