So, let's start by asking ‘Why do we need protective coatings?’
From towering skyscrapers to fleets of railcars and vast industrial complexes, every structure or asset we build faces an ongoing battle with nature. Steel rusts, concrete cracks, and environmental exposure—water, sun, or fluctuating temperatures—accelerate the deterioration process over time.
This is where protective coatings come in.
Coatings act as shields, preserving the structural integrity of the materials they protect and extending the lifecycle of assets. They delay the need for repairs and replacements, ensuring that essential infrastructure remains fully operational. TriFLEX™, our newest addition to the Advanced Polymer Coatings lineup, takes this protection to another level, delivering enhanced durability, flexibility, and resistance to harsh weather through its innovative triple resin technology.
So, what makes TriFLEX™ unique?
The allure of TriFLEX™ lies in its distinctive triple resin system, an innovation that redefines what's possible in the world of protective coatings. Developed in close collaboration with global leaders in the chemical sector, APC’s R&D team of chemists worked hand in hand with various resin and polymer manufacturers to create this industry-first combination of unique properties. Unlike conventional coatings that rely on a single resin, TriFLEX™ leverages the power of three distinct resins, bringing unique benefits that, when combined, cohesively build on top of each other to offer superior performance.
Let's dive into the resin systems and their properties.
Chapters
Chapter 1
Resin 1: Polyurethane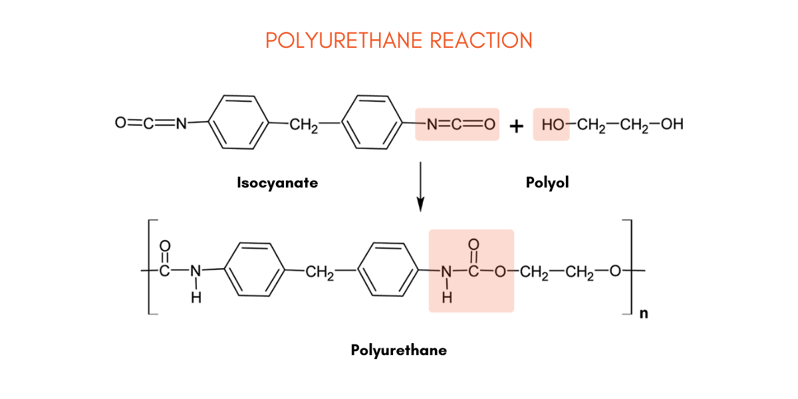
image credit: The condensation polymerisation of an isocyanate (R’-(N=C=O)n) and a polyol (R-(OH)n) to form polyurethane, Lawrence Industries: The chemistry of polyurethanes
Polyurethane is a crucial part of the TriFLEX™ coating system, providing excellent chemical resistance, UV stability, and overall weather resilience. This advanced resin offers superior protection, especially in harsh environments like railcars and industrial assets. In TriFLEX™'s case, the polyurethane resin enhances the coating's durability, longevity, and overall cost efficiency.
Chemical Resistance: Polyurethane's chemical structure makes it highly resistant to a wide range of chemicals, solvents, and environmental pollutants. In industries such as rail transportation, railcars are often exposed to corrosive materials, atmospheric moisture, oils, and other chemicals that can significantly degrade standard coating offerings. Polyurethane forms a strong barrier that prevents the infiltration of these damaging substances, ensuring that the coated surfaces remain intact and free from corrosion for extended periods. This characteristic is particularly crucial for railcar owners and lessors who need to protect their assets from costly repairs and downtime associated with chemical degradation. Polyurethane's strong chemical resistance ensures that the coating maintains its structural integrity and aesthetic appearance despite prolonged exposure to aggressive environments.
UV Stability: Polyurethane is also well-known for its excellent resistance to UV radiation, crucial for coatings exposed to sunlight. Over time, UV radiation can cause significant damage to external coatings, such as fading, yellowing, chalking, and loss of gloss, which can reduce the asset's visual appeal and weaken the protective layer, leading to cracks, peeling, and surface corrosion.
The polyurethane resin in TriFLEX™ has been specifically chosen to resist UV radiation, ensuring the coating retains its original appearance throughout the intended service life, including gloss and color. UV stability is particularly valuable in railcar applications where the assets are often stored outdoors and exposed to direct sunlight for prolonged periods. The coating will not chalk when exposed to UV, extending the corrosion resistance and lifetime of the coating, which is a significant drawback in standard epoxy coatings.
Weatherability: Polyurethane offers exceptional weather resilience, in addition to its chemical resistance and UV stability, making it suitable for a wide range of climates and environmental conditions. Whether it's extreme heat, cold, or high humidity, polyurethane coatings are designed to withstand temperature fluctuations without cracking, blistering, or degrading.
This weather resistance means longer intervals between maintenance cycles for railcars and other industrial assets, as the coating will remain intact despite exposure to severe weather patterns. The coating's flexibility also ensures that it can expand and contract with the substrate as temperatures rise and fall, preventing cracking or other failures that might occur with less resilient materials.
The TriFLEX™ coating system offers an extended lifespan and reduced lifecycle costs. Compared to traditional coatings that last about 10 to 15 years, TriFLEX™ can endure up to 25 years in a C4 environment with proper maintenance due to polyurethane's durability and resistance to wear. This longevity significantly reduces maintenance and repainting costs for railcar owners and industrial asset managers, making it a worthwhile long term investment.
Polyurethane's excellent abrasion resistance also ensures that the coating can withstand the impacts and wear associated with loading, unloading, and transporting heavy materials.
Polyurethane coatings are highly valued in the industrial sector for their versatility. They can be used in various applications beyond railcars, including pipelines, storage tanks, and machinery. This makes TriFLEX™ an ideal choice for asset managers seeking to protect their investments while reducing the long-term costs associated with maintaining large fleets of vehicles or industrial equipment.
Polyurethane's role in the TriFLEX™ coating system extends beyond basic surface protection. Its chemical resistance, UV stability, and weather resilience make it essential for industries that need durable and cost-effective coating solutions. With a service life of up to 25 years, polyurethane-enhanced coatings greatly enhance traditional systems, offering railcar owners, lessors, and industrial asset managers a solution that guarantees long-term performance while reducing maintenance costs.
Chapter 2
Resin 2: Polyaspartic
image credit: Polyaspartic coatings technology, ASI Adhesives & Sealants In
The second resin system, polyaspartic resin, is a crucial component of the TriFLEX™ coating system. It is known for its fast-curing properties, which significantly reduce downtime during application, making it highly sought after in industries where time is critical. This resin enhances the overall performance of the TriFLEX™ coating system by combining rapid application and curing times with durability, chemical resistance, and weather protection.
Polyaspartic resin offers a significant advantage in its rapid drying and curing capabilities. Unlike traditional, standalone epoxy or polyurethane coatings, which may take several days to cure fully, polyaspartics can cure in as little as 1-3 hours, depending on environmental conditions. This quick curing time saves significant time for large-scale applications, such as railcars or industrial equipment.
Every hour a railcar is out of service in the industry represents potential lost revenue. TriFLEX™, leveraging its polyaspartic resin, can quickly return assets to service, leading to less downtime, reduced labor costs, and increased operational efficiency compared to traditional coating systems that may require extended drying periods between coats. Ultimately, this leads to longer project timelines and more significant interruptions in the availability of railcars or other industrial assets.
The fast turnaround provided by the polyaspartic resin is especially beneficial for companies operating large railcar fleets by minimizing the downtime associated with maintenance or re-coating operations, ensuring that assets are out of service for as short as possible.
Increased Application Efficiency: Coatings containing polyaspartic resin can be applied in a single, thick coat, eliminating the need for multiple layers and accelerating the entire application process. Traditional coating systems often require multiple thin layers to achieve the same level of coverage and protection, and subsequently, each layer needs to dry before the next is applied, extending the project timeline and increasing labor costs and the risk of defects if the environmental conditions are not optimal.
Polyaspartic resin enables the application of high-build coatings in fewer steps, resulting in faster job completion without compromising performance. This makes polyaspartic resin well-suited for large surfaces, such as the exteriors of railcars or industrial tanks, where labor and time efficiency are crucial.
Ensuring Durability: Polyaspartic resin cures quickly without compromising durability or performance. It offers excellent abrasion resistance, chemical resistance, and UV stability, making it a versatile choice for outdoor applications, including railcar exteriors that are continuously exposed to the elements.
One common concern with fast-curing coatings is that they may sacrifice long-term performance for speed. However, polyaspartic resins used in TriFLEX™ retain high-performance standards, providing a robust and long-lasting barrier against weathering, UV rays, and chemical exposure and making it suitable for protective and decorative applications.
Cost-Effectiveness and ROI: Reducing application time directly impacts cost-effectiveness. It requires fewer labor hours and reduces downtime for railcars or industrial equipment, allowing businesses to return their assets to operational status more quickly. This leads to faster project completion and lower labor costs, resulting in immediate cost savings.
In the long term, the durability and protective properties of the polyaspartic resin inside TriFLEX™ ensure that the coating remains intact and functional for extended periods, reducing the need for frequent re-coating or maintenance and leading to further cost savings over the asset's life. Compared to traditional, standalone epoxy or polyurethane systems that may require more frequent maintenance cycles, polyaspartic coatings, like the resin system in TriFLEX™, offer a higher return on investment (ROI) over time.
For railcar owners, this means fewer interruptions in service for re-coating and lower lifecycle costs while still benefiting from the high level of protection that the coating provides. The combination of rapid application and long-term durability makes polyaspartic resin an ideal choice for industries where time equals money.
Environmental Benefits: Polyaspartic resins also offer environmental advantages as they often have low volatile organic compound (VOC) emissions, which is increasingly important as industries strive to meet stringent environmental regulations. The fast-curing time further reduces the environmental impact by decreasing the time when harmful emissions could be released into the atmosphere.
Additionally, because polyaspartic resins are durable and require fewer maintenance interventions, they reduce the overall consumption of coating materials over time, contributing to the asset owner's smaller environmental footprint.
Versatility Across Industries: While polyaspartic resins are particularly beneficial in the rail industry due to the need for fast turnaround times, their versatility also makes them ideal for various other industrial applications like pipelines, storage tanks, machinery, and even flooring systems in high-traffic areas. In each of these cases, the ability to apply a fast-curing, highly durable coating translates into less downtime and lower maintenance costs, making polyaspartic an attractive option across a range of industries.
For railcar exteriors, where the environment can be especially harsh, polyaspartic's flexibility, durability, and application speed make it an optimal choice due to the resin's ability to cure quickly in high and low temperatures ensures that the coating can be applied efficiently, regardless of the time of year or climate.
Adding polyaspartic resin to the TriFLEX™ coating system significantly increases its value for industries where minimizing downtime is crucial. With industry-leading drying times, polyaspartic resins allow for faster asset turnaround, enabling businesses to keep their railcars and industrial equipment in service and generate revenue.
Chapter 3
Resin 3: Proprietary Polymer Blend
The third resin in TriFLEX™'s formulation is a proprietary polymer blend that, by design, sets it apart from other coatings in the industry. This unique blend is designed to provide enhanced impact resistance, corrosion protection, and, most notably, flexibility. These combined properties enable the TriFLEX™ coating system to perform exceptionally well under the demanding conditions faced by railcars and other industrial assets where protective coatings are constantly challenged by physical stress and environmental factors.
Impact and Corrosion Protection: One significant advantage of this unique polymer blend is its impact resistance. Railcars and other heavy industrial equipment are frequently exposed to physical forces such as vibrations, collisions, and impacts during transportation and operation. Conventional coatings may chip, crack, or deteriorate under such conditions, leaving the underlying surface susceptible to damage. However, the unique polymer blend used in TriFLEX™ absorbs and disperses these forces, maintaining the integrity of the coating and reducing the likelihood of localized failures.
In addition to impact resistance, this polymer blend offers exceptional corrosion protection, particularly important for assets exposed to harsh environmental conditions such as moisture, chemicals, and fluctuating temperatures. Corrosion is a primary concern for railcars and industrial infrastructure because even minor breaches in the coating can result in rust formation, weakening the surface and compromising the structural integrity of the asset over time. The unique polymer blend creates a continuous, impenetrable barrier that shields metal surfaces from oxidation and chemical exposure, prolonging the life of the coated asset.
Maintaining Coating Integrity and Longevity: The flexibility provided by this polymer blend also plays a significant role in maintaining the long-term integrity of the TriFLEX™ coating system. Coatings that crack under stress expose the substrate to damage and create weak points in the protective barrier, accelerating wear and tear. Once a coating begins to degrade, its effectiveness diminishes rapidly, requiring maintenance, repairs, or even complete reapplication to restore the asset's protection.
TriFLEX™'s proprietary blend mitigates this issue by allowing the coating to shift and adapt to surface movement without compromising its structure. This ensures that the protective barrier remains fully functional for much longer than traditional coatings, reducing the frequency and cost of maintenance over the asset's life cycle.
This ability to remain flexible yet durable improves performance in environments where other coatings might fail. For example, traditional coatings often cannot cope with the added strain in coastal regions or industrial sites where temperature changes and humidity levels fluctuate. TriFLEX™, however, is designed to perform optimally in such environments, maintaining its resistance to corrosion, weathering, and physical damage over time.
The coating's flexibility is crucial in industries like rail transportation, where metal railcars and industrial assets are constantly in motion and exposed to vibration and varying environmental conditions. TriFLEX™'s unique polymer blend allows the coating to bend and flex with the metal surface, offering a protective shield that is less likely to degrade over time. This ensures the asset is shielded from physical damage and corrosive elements.
This flexibility is particularly valuable for railcars, which often experience impacts during coupling, decoupling, and in-transit operations. Traditional coatings may chip or crack under such stresses, leading to rust and corrosion of the metal underneath. However, TriFLEX™'s impact resistance and flexibility ensure that the coating remains intact even under high-stress conditions, providing superior longevity and durability.
Cost Savings Through Reduced Maintenance: One significant benefit of this unique polymer blend is the potential for cost savings. The coating can withstand physical and environmental stresses without cracking or losing adhesion, requiring fewer repairs and maintenance over its service life. This allows railcar owners and operators to keep their assets in service for extended periods, reducing both the direct costs of maintenance and the indirect costs of downtime associated with taking assets out of operation for repairs.
For industrial and railcar fleet owners, the reduced need for re-coating and maintenance results in lower lifecycle costs for their assets. This leads to a higher return on investment (ROI) over time, as the long-lasting performance of the TriFLEX™ coating system reduces the frequency of costly interventions and extends the asset's useful life.
Chapter 4
The Triple Resin Advantage: More Than Just Protection
One of the biggest challenges in the protective coating industry is finding the right balance between coating properties, such as durability and flexibility. Traditionally, choosing a protective coating meant compromising on one category to excel in anther, leading to difficult trade-offs in performance. However, with TriFLEX™'s triple resin technology, you don't have to make that choice.
With TriFLEX™’s unique triple resin technology, you get one complete coating system without sacrifices:
- Strength to withstand abrasions, impacts, and environmental stresses.
- Flexibility to handle temperature shifts without cracking or peeling.
- Superior UV protection to keep surfaces looking pristine and performing optimally for longer.
This balance results in fewer maintenance cycles, less downtime, and lower costs over the asset's lifespan for railcar owners and leasing companies. TriFLEX™ offers the long-term value industries need to protect their fleets and infrastructure without being burdened by constant upkeep.
Conclusion
Whether you manage a fleet of railcars, oversee an industrial asset, or work as an application specialist, TriFLEX™ offers an easy-to-apply and cost-effective solution that simplifies protective coatings and provides reliable, long-lasting performance with an innovative design.
For more information on TriFLEX™, contact a member of our Industrial Sales Team and check out www.adv-polymer.com.