To perform at optimal capability, the linings used in these diverse facilities must correlate with the environmental conditions present.
Specifically, in the power generation market, internal lining systems may be designed to protect against abrasion, chemical corrosion and heat — conditions that exist, for example, in the abrasive environment of a coal handling facility or the highly corrosive environment of an absorber/scrubber or in facilities for waste recovery and water treatment.
At APC, we have developed coating formulations that are ideal for use at power plants. The coatings are based on unique, patented cross-linking polymer system that creates a very dense, tightly knit chemical structure, with a virtually impenetrable surface.
In this article, we review scenarios (with images) where coatings are used to protect against high-temperature, and corrosive environments.
Specialized Protection Needs
Flue gas desulfurization (FGD) units pose a unique challenge in power plants. Scrubbers lined with stainless steel are prone to corrosion. Acid condensation formed during the FGD process — along with abrasion, pit corrosion and chlorides — is a typical source of failure. No two scrubbers are alike. The elevated temperatures, dew point, wet-dry cycles, gas velocity, high sulfate solutions, fluorides and chlorides that may be present will accelerate pitting and crevice corrosion, requiring imminent repairs to the process and structural vessels.
In a wet FGD unit, four areas are prone to corrosion due to constituents of the environment: the 1) absorber/scrubber, 2) outlet duct, 3) mix chamber and 4) stack. Each one of these areas is subjected to different pressures, such as high operating temperatures, highly acidic surroundings and abrasive environments, among others. To protect all of these areas from corrosion, a lining that provides a combination of abrasion, chemical and permeation resistance is needed.
Figure 1. Power plants have many areas throughout the facility that require high-performance coatings protection from corrosive environments.
A vinyl ester lining is sometimes applied in these areas at 30 to 60 mils. The disadvantages of this type of lining system are:
- high styrene content (extremely flammable and toxic during application and cure)
- high cure shrinkage (causing cracking and brittleness)
- sensitivity to atmospheric moisture and temperature, causing the lining to have problems curing when atmospheric conditions are not right
- inability to be repaired in the field
- incompatibility with other coatings, making it difficult to bond to dissimilar and already-cured materials
- if an applicator adds too much thinner, it causes the lining to lose strength.
Other lining choices include troweled thick-film vinyl esters, spray or troweled flake systems, sprayed-on epoxy, heavy-duty mortar laminate systems with abrasion resistant aggregate and vulcanized rubber. FGD and duct systems can vary depending on system design and fuel source. These conditions can include:
- SO2
- Condensing hot H2SO4 (sulfuric acid)
- Calcium sulfate/lime slurry
- High temperature/upsetting conditions
- Highly abrasive gas
- Substrate movement due to unit cycling/ vibration
Figure 2. Severe pipe and scrubber corrosion (top image) caused by an acidic gas and slurry mixture is protected with a ChemLINE lining application (bottom image).
Figure 3. Carbon steel stack (top left image) at this power facility has its previous delaminated and corroded lining removed (top right image) and is then re-lined with ChemLINE (bottom image) to protect against the high-temperature, corrosive environment.
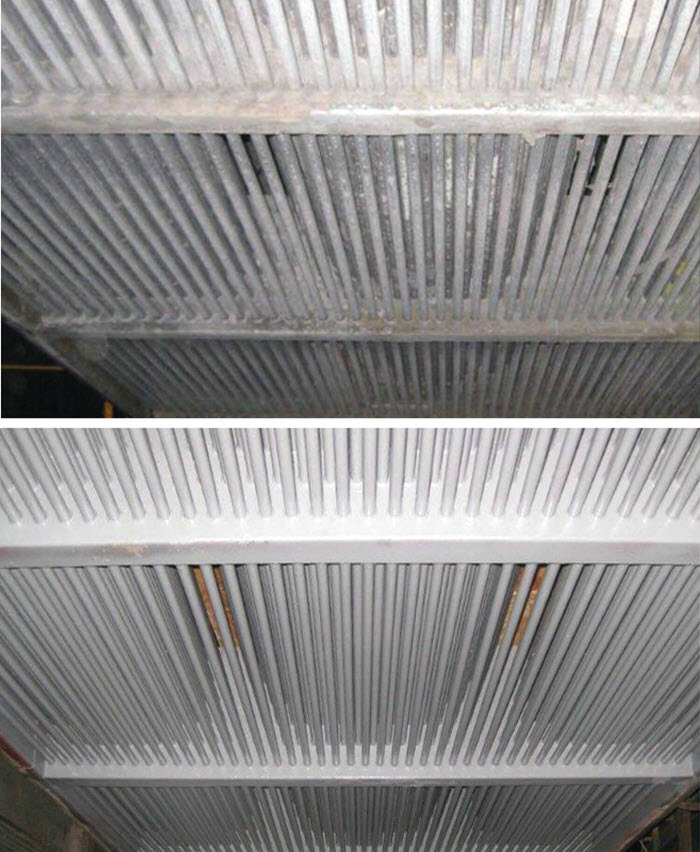
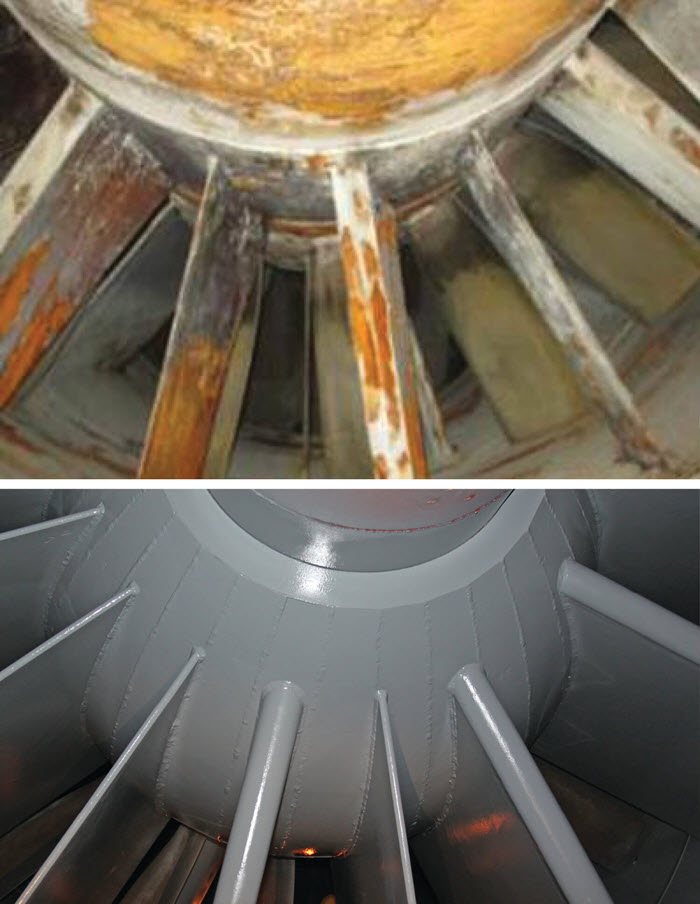
One Lining For Multiple Conditions
High-build vinyl ester linings are a traditional choice for power facility ductwork, as their low permeability prevents the absorption of hot condensing flue gases that attack the lining substrate. The permeation rate of ChemLINE, is 0.0000 grams per square foot per 7 days per inch of thickness.
Conclusion
ChemLINE offers a thin film option at 12 to 14 mils that provides excellent resistance to chemicals, hot flue gas conditions and extreme abrasion. It also offers flexibility to handle substrate movement not found in vinyl esters.
At APC, we understand the challenges you face every day. We will always continue to develop and improve our coatings and technologies.
As a quality, premier coatings solutions provider we provide innovative, value-added coatings for the protection of your assets.