Originally constructed from wood, the first tank car has dramatically transformed into the massive steel structure known today to transport liquid products and chemicals worldwide.
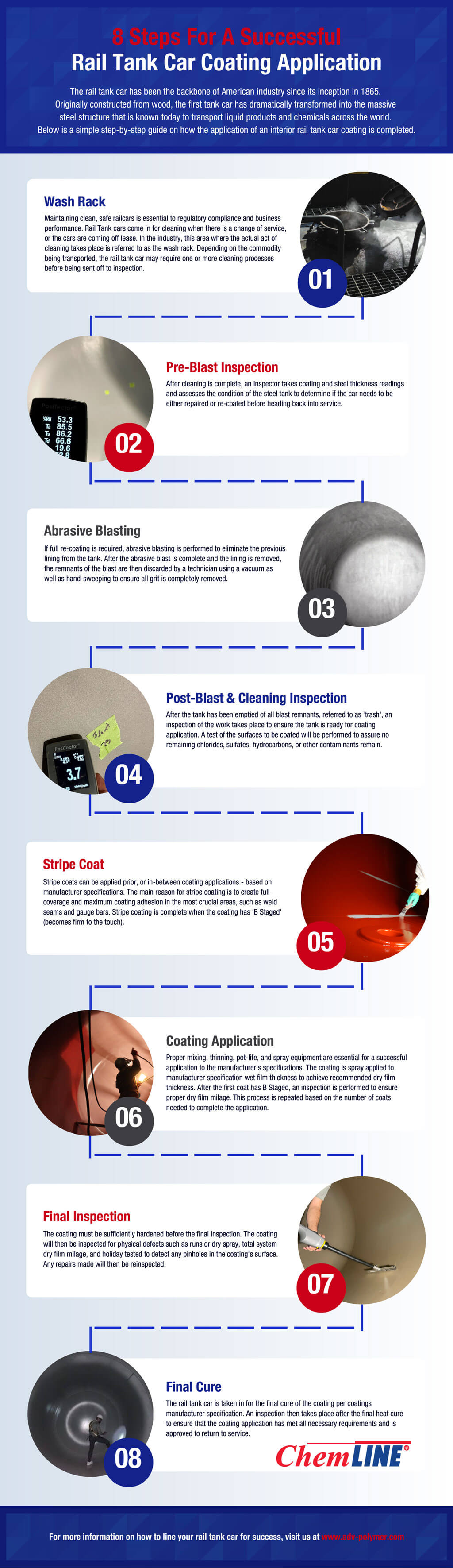
1. Wash Rack
When a rail tank car arrives at the coating shop, the first stage is cleaning the interior of the car—typically, the area of the shop where this takes place is referred to as the "Wash Rack."
Maintaining clean, safe railcars is essential to regulatory compliance and business performance. Rail tank cars come in for cleaning when there is a service change, or the cars are coming off lease.
Depending on the commodity being transported, the rail tank car may require one or more cleaning processes before being inspected.
2. Pre-Blast Inspection
a. After the cleaning is complete, an inspection takes place. The inspector takes coating and steel thickness readings, assesses the steel tank's condition, and determines if the car needs to be repaired or re-coated before returning to service. This step is discussed with the rail tank car's customer or owner.
b. Depending on the condition of the lining, a determination is made to spot repair or completely re-line the car.
3. Abrasive Blasting
If spot repairs are to be made, the shop should follow the spot repair recommendations of the original lining manufacturer and repair with the same lining material.
If full-recoating is required, abrasive blasting is performed to eliminate the previous lining from the tank.
a. With certain coatings and service conditions, a pre-bake is done to blister the coating to make abrasive blasting and removal of that coating easier.
b. The blast remnants are then removed from the rail tank car through a technician entering the tank and vacuuming the grit and large particles. The technician will hand-remove the smaller remnants from the tank with a hand broom or brush.
4. Post-Blast & Cleaning Inspection
a. After the tank has been emptied of all blast remnants, sometimes referred to as ‘trash,’ an inspection of the work then takes place to ensure the tank is ready for coating application.
b. The surfaces to be coated will be tested to assure no remaining chlorides, sulfates, hydrocarbons, or other contaminants remain. If contaminants are found, re-cleaning and re-blasting will be done to achieve acceptable results.
Rail Tank Cars: Safety and Utilization
In the guide, you’ll learn who the key players are in the manufacturing of rail tank cars, lining versatility that
accompanies them, safeguarding your tank cars, how one company eliminated “hydrogen grooving,” and the future of the market.
Get the PDF version to save to your desktop and read it when it's convenient for you. (No email required):
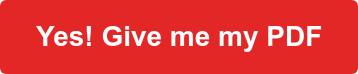
5. Stripe Coat
a. A stripe coat is usually applied before any spray application is done; however, stripe coats can also be completed in-between coats.
b. It's essential to thoroughly read and follow the application documents when applying a coating to ensure the process is done according to each manufacturer's specific standards because coatings may apply and cure at different intervals. The stripe coat is hand-applied using a paintbrush.
c. The main reason for stripe coating is to create full coverage and maximum coating adhesion in the most crucial areas, such as weld seams or gauge bars in a rail tank car.
d. Stripe coating is complete when the coating has “B Staged” (becomes firm to the touch).
e. If a stripe coat is done before the first application of coatings, an inspection of the stripe coat is performed.
6. Coating Application
a. It’s important to carefully follow the manufacturer's specifications before the first coat is applied. Proper mixing, thinning, pot-life, and spray equipment are essential for a successful application.
b. Coating is spray-applied to manufacturer specification wet film thickness to achieve recommended dry film thickness (DFT). During the coating process, wet film thickness testing is performed to ensure proper DFT is achieved.
c. After the first coat is applied and has reached the proper B Stage, an inspection is performed to check for appropriate dry film milage.
d. Repeat the application steps per the recommended number of coats required by the coatings manufacturer.
7. Final Inspection
a. The coating must be sufficiently hardened before performing this step.
b.The coating will be inspected for physical defects such as runs or dry spray, total system dry film milage, and holiday tested to detect any pinholes in the surface of the coating.
c. Pinholes and damaged areas must be repaired and corrected following the lining manufacturer’s procedures.
d. Repaired areas will be reinspected after repairs are completed.
e. For heat-cured coatings, the inspection and repairs should be made before final heat curing.
8. Final Cure
a. The rail tank car is taken in for the final coating cure per manufacturer specification.
b. An inspection takes place after the final heat cure to ensure that the rail tank car coating application has met all requirements and is approved for service.
Conclusion
It is wise to consider a universal lining to ensure greater flexibility in the range of chemicals handled by one tank. Extensive testing and years of field experience have shown that ChemLINE® successfully protects tanks against more types of chemicals and environmental influences than stainless steel, phenolic epoxies, and other conventional coatings.
ChemLINE® can save you tens of thousands of dollars in labor, materials, and repairs to avoid the need to re-coat and preserve the integrity and longevity of your tanks and the purity of the contained chemicals.
An exceptional rail tank lining creates an impenetrable barrier and prevents costly hiccups.
Increase longevity and have confidence in your rail cars performance with ChemLINE®
Featured image: Tomasz Wyszolmirski/Shutterstock.com