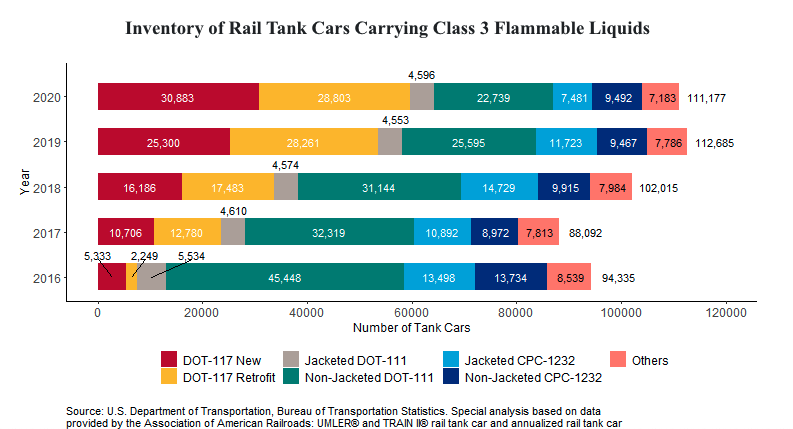
U.S Department of Transportation (Federal Railroad Administration) reports:
"As tank cars are the predominant vehicles for carrying hazardous material shipments, FRA has prepared Tank car guidance materials on maintaining, operating, and securing this rail equipment:"
- Ensuring Tank Car Safety
- Tank Car Committee Handouts
- Suggestions for Effective Railroad Tank Car Loading/Unloading Training Programs
The rail tank car hauled liquids since oil was first discovered in the 1860s. Their characteristics, with their different commodities being transported, make them unique.
Chapters
- 1Rail Tank Cars Timeline
- 2Who are the Key Players in the Railway Tank Car Market?
- 3What are the Different Types of Freight Cars Today?
- 4Lining Versatility for Rail Tank Cars to Enhance Operations
- 5Top Considerations to Safeguard Rail Tank Cars
- 6Rail Tank Car Application [Case Study]
- 7Future Rail Tank Car Market Outlook
Chapter 1
Rail Tank Cars Timeline
Let's start things off with a quick timeline of the industry.
- 1865: Charles P. Hatch of the Empire Transportation Company invents the railroad tank car. Flatcars with banded wooden planks or decking mounted on top were used for the first time to transport crude oil from Pennsylvania during the Pennsylvanian oil rush.
- 1869: Wrought iron tanks, with an approximate capacity of 3,500 US gallons per car, replace wooden containers.
- 1888: Tank-car manufacturers sell units directly to the oil companies, with sizes ranging from 6,000 to 10,000 US gallons.
- 1903: Tank-car companies develop construction safety standards. More than 10,000 tank cars are in operation.
- 1915: A classification system is produced by the tank-car industry to ensure the correct match of car type to the shipped product. Approximately 50,000 tank cars are in use.
- 1930: 140,000 tank cars transport 103 commodities.
- The 1940s: Virtually every tank car engages in oil transport supporting the war effort.
- 1945–1950: Welding replaces riveting in car construction (both underframes and tanks) for the major manufacturers, including American Car & Foundry and General American.
- 1950: Pipelines and tank trucks competed for the liquid transport business.
- 1955: Intermodal freight — the movement of containers and highway trailers by rail —
is reported as a separate category of cargo for the first time. In that year,
railroads moved 168,000 carloads of trailers and containers. - 1963: The Union Tank Car Company introduces the "Whale Belly" tank car.
- 1980: Congress passes the Staggers Rail Act, reducing the Interstate Commerce
Commission's regulatory authority over railroads and sparking competition that
stimulates advances in technology and a restructuring of the industry. This includes the
creation of hundreds of new shortlines and regional railroads. - 2017: U.S. railroads originate 13.7 million intermodal containers and trailers, setting a
new annual record. In 1990, containers accounted for 44 percent of intermodal
traffic. By 2000, the share was 69 percent. In 2017, it was 91 percent.
Containers are generally more efficient than trailers, in part because they can be
“double-stacked." - 2018: Freight was steady in 2018, with carloads up 3.9 percent. [source] 80,298 tank cars were used to transport flammable liquids. [source]
Basic Types of Tank Cars
All rail tank cars are built to standards and requirements by the U.S. Department of Transportation (DOT) and the Association of American Railroads (AAR).
Railway Supply Institute cites,"A railcar with a tank for its body consists of a shell and heads together with connections welded directly to it and used to transport liquids, solids, and liquefied gases. By AAR specifications, “tank” means “tank car tank.” The head of a tank is one of the end closures. Tank cars may be pressure or non-pressure and are often equipped with special equipment to enhance their usefulness for handling specific commodities. For pressure class tank cars, the tank includes the manway nozzle as well."
There are generally two basic types of tank cars:
1. General-purpose - are non-pressure cars that can be used to carry any kind of material. They can be referred to as general service or low-pressure tank cars.
2. Pressure tank cars transport compressed liquefied gases under pressure and some low-pressure, high-hazard materials. They are built with thicker tanks to withstand higher internal pressures. [source]
Resources:
Chronology of Railroading in America
Chapter 2
Who Are the Key Players in the Railway Tank Car Market?
If you are in the market to lease a tank car or need services, credentials are everything. What makes a key player in the railway tank car market?
- providing value
- identifying customer needs
- responsibility
- and recommendations by Market watch
The Top Key Players (in no particular order):
1. Trinity Industries - Dallas, TX
Trinity Industries - is a premier provider of railcar products and services in North America. TrinityRail is a leader in the manufacturing, leasing, and maintenance of various railcar product segments, notably tank cars.
2. Greenbrier - Lake Oswego, OR
Greenbrier is a leading international equipment supplier and services to the freight rail transportation markets. They "operate an integrated business model in North America that combines freight car manufacturing, wheel services, repair, refurbishment, retrofitting, parts, leasing and fleet management services."
3. National Steel Car - Hamilton, ON
National Steel Car has earned a reputation as North America’s leading railroad freight and tank car manufacturer. They are the "only North American railcar company certified ISO 9001:2015."
4. Union Tank Car - Chicago, IL
UTLX is the "industry-leading supplier of general-purpose and pressure tank cars and plastics-covered hopper cars for bulk shippers. At Union Tank Car Company's core are railroad tank car leasing, manufacturing, and repair operations."
5. American Railcar Industries - St. Charles, MO
American Railcar Industries offers railcar leasing and services. "ARI will work with you and provide support throughout the railcar lifecycle."
6. GATX Corporation - Chicago, IL
GATX "owns, manages, or is interested in more than 118,000 railcars and over 600 locomotives." They are a leading global railcar lessor.
Chapter 3
What are the Different Types of Freight Cars Today
It's simple, depending on your needs.
It will determine the type of freight car you'll require.
source: North American Railcar Review 2022
The fleet increased slightly, driven by the expansion in covered hoppers and tanks.
Moving on, the different types of rail cars:
Tanks - In 2014, the Railway Supply Institute Committee on Tank Cars (RSICTC) recommended that DOT adopt tank car standards for newly built tank cars assigned to crude oil and ethanol service. Insulation (to maintain the appropriate temperature), thermal blanket (for fire protection), and top fittings (with relief valves) were an effort to revise the tank car standards.
resource with images: Tank Car Standard
Hoppers - a type of railroad freight car or container used to transport loose, bulk commodities such as grain or coal. It is typically a container that tapers downward and can discharge its contents at the bottom.
Gondola - is an open-topped rail vehicle also used for transporting loose bulk materials. "Because of their low sidewalls, gondolas are also suitable for carriage such high-density cargoes as steel plates or coils or bulky items such as prefabricated sections of rail track." [source]
Flats - is a piece of railroad rolling stock that consists of an open, flat deck mounted on a pair of trucks, one at each end containing four or six wheels. Flatcars are used for loads too large or clumsy to load in enclosed cars such as boxcars.
Covered Hoppers - equipped with a roof, are used as a hopper. The only difference is that the cover protects the loads from the weather.
Box Car- is a railroad car enclosed and generally used to carry freight. The boxcar is probably the most versatile since it can carry most loads.
The longevity of assets is crucial in the profit margins for tank container operators and lessors. Especially for tank containers carrying aggressive cargo, a high-performance lining system is critical to prevent corrosion and extend the container's lifetime.
Chapter 4
Lining Versatility for Rail Tank Cars to Enhance Operations
- petroleum/crude
- ethyl alcohol
- sodium compounds
- petroleum by-products
- LPG
- sulfuric acid 93-100 percent
Chapter 5
Top Considerations to Safeguard Rail Tank Cars
1. Chemical Resistance to Exposures and Temperatures
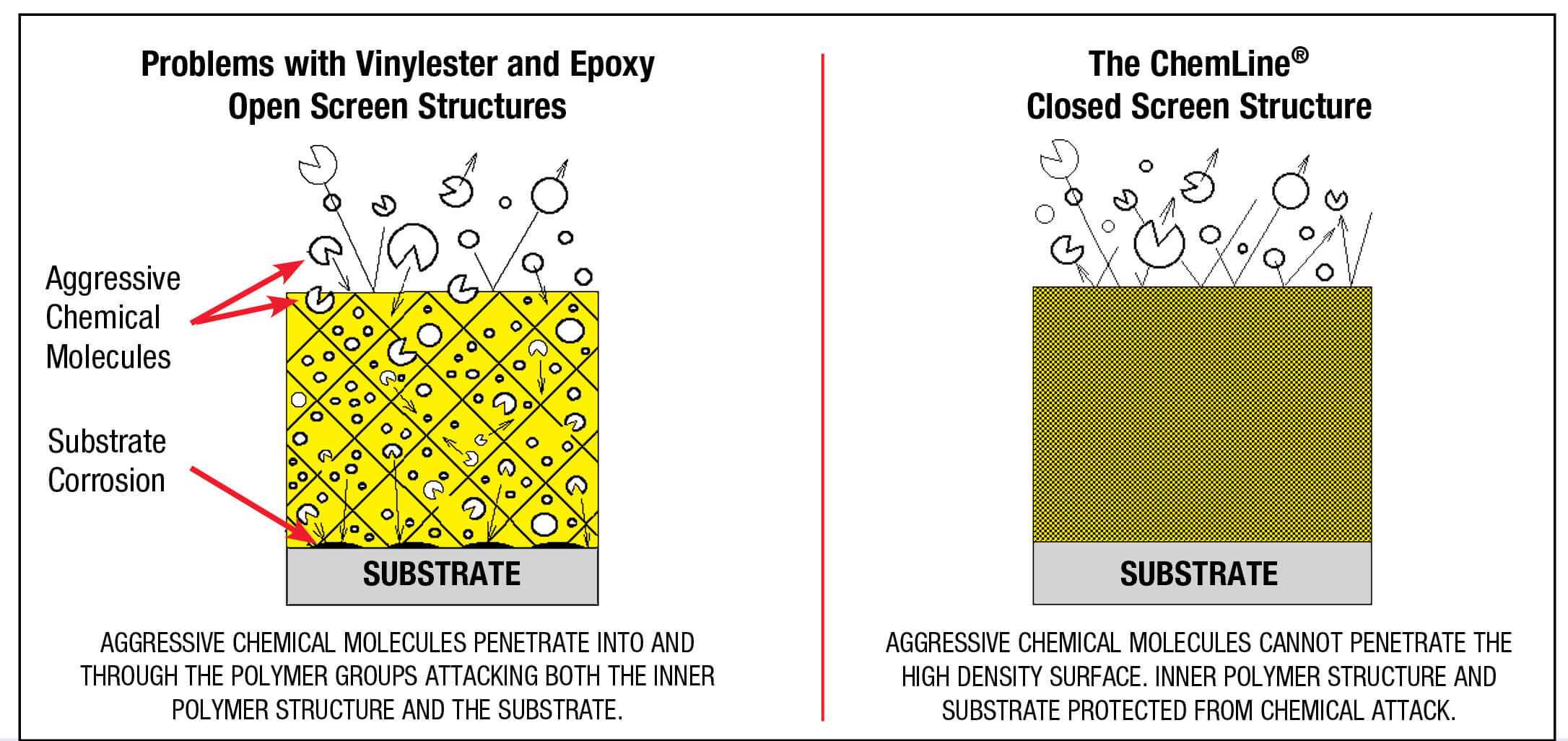
2. Food-Grade Approval for Safety (GRAS)
3. Product Purity to Reduce Cargo Contamination
4. Easy Cleaning for Faster Return to Service
5. Proper Application to Deliver Abrasion-Resistant Solution
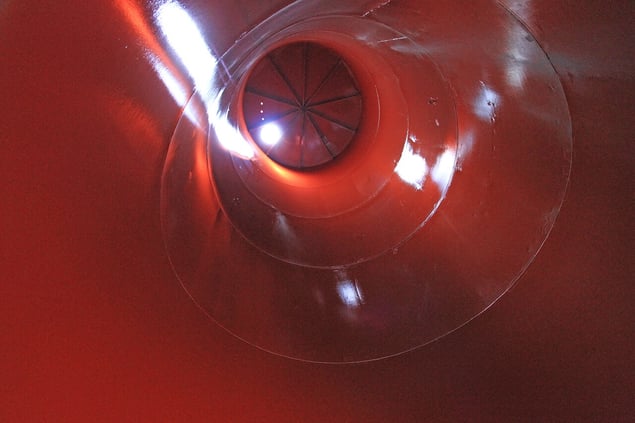
6. Proven Field Performance for Best Results
Chapter 6
Rail Tank Car Application [Case Study]
So here's the deal:
It's time to look at the results:
In this section, you'll see how Solvay USA went from hydrogen grooving to an internal tank corrosion protection in a few days with their rail tank cars swiftly put back into service.
Case Study
How Solvay USA used ChemLINE® to Extend the Service Life of its Rail Tank Cars
Solvay USA Inc. is a world-leading producer of essential chemicals, including 99+% sulfuric acid and other products.
Problem: a corrosion problem with rail tank cars carrying 99+% sulfuric acid and spent alkylation sulfuric acid.
Corrosion occurs when sulfuric acid produces hydrogen gas. As the gas moves upward in the rail car, it erodes the steel surface, causing a grooving pattern. Unlined tank rail cars are not usually retired from service due to uniform corrosion but deep hydrogen grooving.
The tank cars were brought to Seaboard Railcar Repair in Hugo, OK, where an inspection showed some pitting and other problems.
Solution:
1. Seaboard prepped the internal surface through grit blasting to clean out contaminants and pitting, grinding the sharp edges caused by grooving, and repairing areas as needed. The tank cars would be structurally suitable for the application.
2. Next, a grey base coat of ChemLINE® 784 ES (formerly named ChemLINE® 784/32) was applied, followed by a red topcoat. The tanks were then forced hot air-cured, per the coating manufacturer’s specifications.
The ChemLINE® 784 ES's higher cross-link density means:
- Higher chemical resistance
- Higher temperature resistance
- Higher reactivity at a lower temperature
- Higher resistance to absorption
- Higher toughness
3. The rail tank cars were put back into service within a few days.
One year later, at inspection:
The inspection showed that the overall condition of both rail tank cars was excellent, with the lining intact with no corrosion or grooving observed.
Result: Significant increase in the service life of Solvay USA rail tank cars with ChemLine®
784 ES which will provide tremendous cost savings.
Read the entire case study: Solvay USA uses ChemLINE® 784 ES (784/32) for Sulfuric Acid Service in Rail Tank Cars.
Chapter 7
Future Rail Tank Car Market Outlook
Freightwaves reports:
"There are three broad railroad tank car markets – chemicals, crude oil, and selected agricultural commodities. Across North America, the number of tank cars in the fleet increased from ~300,000 in 2009 to ~432,000 in 2019."
The chemical tank car market comprised roughly 13% of the carloads of rail traffic moved during 2019. Heavy crude oil shipments into the U.S. were the largest crude oil market segment, with approximately 54,000 monthly carloads total.
Railroad tank cars are used to move grain-based energy (ethanol). Railroads move more than 60% of the U.S. ethanol traffic. [source]
The market at this time is uncertain, given the start of 2020. Rail freight will probably continue to remain flat, but time will tell.
Railway Age curated a summary of key takeaways from speakers at REF (Rail Equipment Finance) 2019 that had some insight (before COVID-19). The industry is still faced with challenges, but time will tell. There is hope for market improvement after an overall economic recovery.
resource:
Conclusion
To ensure greater flexibility in the range of chemicals that can be handled by one tank, consider a universal lining. Extensive testing and field experience have shown that ChemLine® successfully protects tanks against more chemicals and environmental influences than stainless steel, phenolic epoxies, and other conventional coatings.
ChemLine® can save you tens of thousands of dollars in labor, materials, and repairs to avoid the need to re-coat and preserve the integrity and longevity of your tanks and the purity of the contained chemicals.
With a top-quality tank lining, you will create an impermeable barrier and prevent costly issues.